Como Implementar a Manutenção Preventiva Preditiva Eficaz
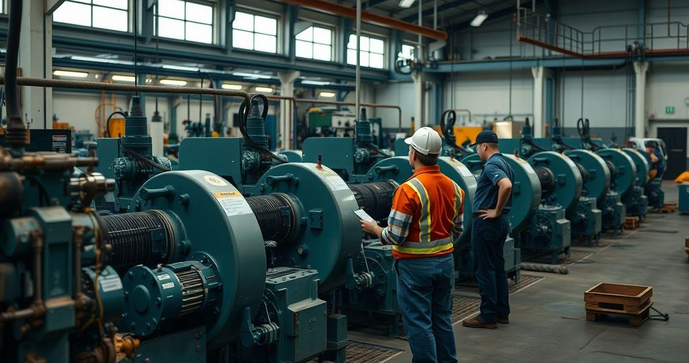
Por: Carol - 24 de Junho de 2025
Entendendo o Conceito de Manutenção Preventiva Preditiva
A manutenção preventiva preditiva é uma abordagem proativa que visa prever e prevenir falhas em equipamentos e sistemas através de análises e monitoramento contínuos. Diferentemente da manutenção corretiva, que intervém apenas após a ocorrência de problemas, este método foca na identificação de ineficiências e na realização de intervenções antes que os danos ocorram.
Esse tipo de manutenção utiliza dados e informações coletadas em tempo real para determinar o estado e a condição dos equipamentos. Técnicas como análise de vibração, termografia e ultrassom são comumente utilizadas para avaliar se uma máquina está funcionando adequadamente ou se há sinais de desgaste.
Uma das principais características da manutenção preventiva preditiva é a busca pela maximização do tempo de atividade dos equipamentos. Ao prever falhas, as empresas podem planejar paradas para manutenção de forma a minimizar impactos na produção e otimizar custos operacionais.
Ademais, essa abordagem permite que as empresas aprimorem suas estratégias de gerenciamento de recursos, direcionando investimentos para o que realmente importa e evitando gastos desnecessários com manutenções emergenciais. Assim, a manutenção preventiva preditiva contribui não só para a eficiência operacional, mas também para a segurança no ambiente de trabalho.
Vantagens da Manutenção Preventiva Preditiva na Indústria
A manutenção preventiva preditiva oferece uma série de vantagens significativas para a indústria, que podem impactar diretamente na eficiência operacional e na redução de custos. Entre os principais benefícios, destaca-se a diminuição de paradas inesperadas, uma vez que as intervenções são realizadas antes que falhas ocorram.
Outro ponto positivo é a otimização da vida útil dos equipamentos. Ao identificar e corrigir problemas em potencial antes que eles se tornem sérios, as empresas podem prolongar a durabilidade de suas máquinas, resultando em menos investimentos em substituições e mais tempo de operação.
Além disso, a manutenção preditiva permite uma melhor alocação de recursos. Com a previsão precisa de manutenções necessárias, as empresas conseguem programar paradas em horários estratégicos, o que auxilia na continuidade das operações e evita interrupções durante períodos críticos de produção.
A aplicação desse tipo de manutenção também se traduz em melhorias na segurança do ambiente de trabalho. Equipamentos deteriorados podem representar riscos significativos. Com a manutenção preventiva preditiva, os riscos são minimizados, garantindo a segurança dos operadores e outros funcionários.
Por fim, a implementação de uma cultura de manutenção preditiva pode proporcionar um aumento na moral da equipe. Funcionários que operam em um ambiente mais seguro e eficiente tendem a estar mais satisfeitos e motivados, o que, por sua vez, se reflete positivamente na produtividade geral da empresa.
Como Escolher Ferramentas e Tecnologias para Implementação
A escolha das ferramentas e tecnologias adequadas para implementar a manutenção preventiva preditiva é crucial para o sucesso dessa estratégia. O primeiro passo é avaliar as necessidades específicas da sua operação, considerando o tipo de equipamento, as condições de operação e o nível de complexidade do processo produtivo.
Uma das principais opções são os Sistemas de Gestão de Manutenção Computadorizados (CMMS), que ajudam a gerenciar e programar atividades de manutenção. Esses sistemas permitem o acompanhamento em tempo real do desempenho dos equipamentos, bem como a geração de relatórios que facilitam a tomada de decisão.
Adicionalmente, ferramentas de monitoramento em tempo real, como sensores de vibração, temperatura e pressão, são essenciais. Esses dispositivos coletam dados contínuos sobre o funcionamento do equipamento, possibilitando a detecção de anomalias antes que causem falhas.
Outro aspecto importante é a integração de tecnologias de análise de dados, como big data e inteligência artificial. Essas tecnologias podem ser utilizadas para interpretar grandes volumes de informações coletadas, auxiliando na previsão de falhas e na definição das melhores práticas de manutenção.
Por fim, é fundamental considerar a possibilidade de treinamento das equipes para o uso eficaz dessas ferramentas. Investir na capacitação de colaboradores garantirá que os sistemas e tecnologias sejam utilizados corretamente, maximizando os benefícios da manutenção preditiva e promovendo uma cultura de melhoria contínua na organização.
Estratégias para Monitoramento e Avaliação de Equipamentos
A eficácia da manutenção preventiva preditiva depende de estratégias eficazes para o monitoramento e avaliação dos equipamentos. Uma abordagem inicial é a definição de indicadores de desempenho chave (KPIs), que ajudarão a medir a eficiência e a condição operacional dos maquinários. Esses KPIs podem incluir taxa de falhas, tempo médio entre falhas (MTBF) e tempo médio para reparo (MTTR).
Uma estratégia eficaz é a implementação de sistemas de monitoramento contínuo. A utilização de sensores para coletar dados em tempo real é fundamental, pois possibilita a detecção precoce de problemas. Sensores de vibração, temperatura e acústicos podem fornecer informações valiosas sobre o funcionamento do equipamento.
Além disso, a realização de análises periódicas, como inspeções visuais e testes de desempenho, deve ser parte integrante da estratégia. Esses check-ups permitem identificar desgaste, corrosão ou outras anomalias que possam impactar a operação do equipamento.
Outra prática recomendada é a utilização de software especializado que agregue dados de diferentes fontes. Programas de análise preditiva podem interpretar dados coletados e gerar relatórios que ajudam na tomada de decisão sobre quando realizar intervenções. Isso garante que as manutenções sejam práticas e baseadas em condições reais de operação.
Por último, é importante fomentar uma cultura de feedback contínuo entre as equipes de operação e manutenção. Estabelecer um canal de comunicação onde os operadores possam relatar anomalias ou sugestões pode resultar em insights valiosos para a avaliação dos equipamentos e melhorias nos processos de manutenção.
Treinamento de Equipes para Práticas de Manutenção Preditiva
O treinamento de equipes é um componente fundamental para a implementação bem-sucedida da manutenção preventiva preditiva. Para que os colaboradores possam operar equipamentos e utilizar ferramentas de monitoramento eficazmente, é imprescindível que recebam uma formação adequada que abranja tanto aspectos técnicos quanto práticas de segurança.
Uma abordagem inicial no treinamento deve ser a conscientização sobre a importância da manutenção preditiva. Os colaboradores precisam entender como essa estratégia contribui para a eficiência operacional, a segurança e a redução de custos, o que pode aumentar a motivação e o engajamento da equipe.
Em seguida, o treinamento deve incluir instruções detalhadas sobre a utilização das ferramentas e tecnologias adotadas. Isso pode envolver sessões práticas onde os funcionários aprendem a operar sistemas de gestão, utilizar sensores de monitoramento e interpretar relatórios de desempenho. Simulações e exercícios práticos podem ser eficazes para reforçar o aprendizado.
Ademais, é importante abordar as melhores práticas em relação à manutenção. Os colaboradores devem ser capacitados a identificar sinais de falhas ou desgastes e a saber como agir quando esses problemas surgirem. Isso inclui a habilidade de realizar inspeções visuais e testes básicos que ajudem a prolongar a vida útil dos equipamentos.
Por fim, promover a cultura de melhoria contínua é vital. Incentivar os funcionários a se manterem atualizados sobre novas tecnologias e práticas de manutenção pode contribuir para um ambiente mais inovador e eficaz. Realizar treinamentos periódicos e workshops também pode mantê-los motivados e sempre prontos para aplicar os conceitos da manutenção preditiva no dia a dia.
Estudos de Caso: Sucesso na Implementação da Manutenção Preditiva
Estudos de caso são essenciais para entender a eficiência e os resultados da implementação da manutenção preventiva preditiva em diferentes setores. Um exemplo notável vem da indústria petroquímica, onde a implementação dessa abordagem levou à redução de 30% no tempo de inatividade não programado.
Através da instalação de sensores em equipamentos críticos, a empresa conseguiu antecipar falhas e realizar manutenções programadas, economizando custos significativos.
Outro caso de sucesso ocorreu em uma fábrica de automóveis, que decidiu adotar a manutenção preditiva em suas linhas de montagem. Ao integrar ferramentas de monitoramento em tempo real e análises preditivas, a empresa conseguiu aumentar a eficiência operacional em 25%. Além disso, a redução nos custos com manutenção emergencial e a melhoria na qualidade da produção foram benefícios adicionais que resultaram dessa mudança.
No setor de energia, uma companhia elétrica implementou práticas de manutenção preditiva em suas turbinas eólicas. Utilizando tecnologias de análise de dados, a empresa conseguiu prever falhas e otimizar a programação de manutenções. O resultado foi um aumento de 15% na produção de energia e uma significativa redução nos custos associados à manutenção corretiva.
Outro exemplo vem de uma planta de papel e celulose que aplicou a manutenção preditiva em suas máquinas de produção. Com a utilização de modelos analíticos e sensores de vibração, foi possível identificar problemas antes de eles afetarem a produção. Essa estratégia resultou em uma queda de 40% nas paradas não programadas, além de aumentar a confiança dos operadores nas máquinas.
Esses estudos de caso ilustram como a manutenção preventiva preditiva pode trazer benefícios tangíveis para diferentes indústrias. A implementação bem-sucedida dessa estratégia não só melhora a eficiência e a produtividade, mas também gera economias significativas, tornando-se uma escolha estratégica para empresas que desejam manter uma vantagem competitiva no mercado.
A implementação da manutenção preventiva preditiva se mostra essencial para as indústrias que buscam otimizar suas operações e reduzir custos.
Os diversos benefícios, que vão desde a diminuição de paradas não programadas até a maximização da vida útil dos equipamentos, destacam a importância dessa abordagem.
Ao capacitar equipes e adotar ferramentas adequadas, as empresas conseguem não apenas manter a eficiência operacional, mas também garantir um ambiente de trabalho mais seguro.
Com estudos de caso que evidenciam seu sucesso, fica claro que investir em manutenção preditiva é um passo decisivo para o futuro competitivo das organizações.